6 Steps to Waterproofing Construction on A Building Site
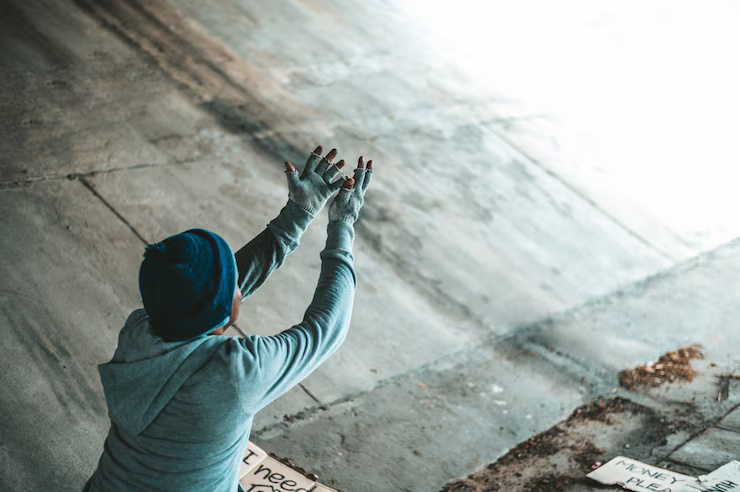
When it comes to construction, one of the most critical but often overlooked aspects is waterproofing construction. We understand that protecting a building site from water infiltration isn’t just about preserving aesthetics—it’s about safeguarding the structural integrity, preventing costly damage, and ensuring a long-lasting build.
Water intrusion can compromise foundations, cause mold growth, and lead to expensive repairs down the line. Proper waterproofing is a proactive step every construction project must prioritize, from the initial groundwork to final touches on the exterior. Based on our years of experience in commercial and industrial construction, we’ve identified six essential steps to waterproofing construction that every builder and project manager should follow.
Step 1: Comprehensive Site Assessment and Planning
Before any waterproofing measures begin, the first step is a thorough assessment of the building site. We emphasize understanding the environmental factors impacting your site. This means analyzing the soil composition, water table level, drainage patterns, and local climate conditions.
For example, a site with clay-heavy soil will retain water differently than sandy soil, requiring different waterproofing strategies. Also, understanding seasonal rainfall and potential flood zones helps us customize solutions. The goal of this step is to develop a waterproofing plan that anticipates water challenges unique to your site.
Planning includes coordination with architects, engineers, and contractors to ensure waterproofing details align with structural design and material selection. A well-planned waterproofing strategy reduces delays and prevents costly rework.
Step 2: Effective Drainage System Installation
Once the site assessment is complete, installing a robust drainage system is crucial. Water must be directed away from the foundation to avoid pooling and infiltration. Michaels Sheet Metal always recommends perimeter drains, such as French drains, that collect groundwater and channel it safely away from the structure.
We also ensure proper grading around the building—landscaping slopes should guide water flow away from the foundation. Temporary drainage solutions may be required during construction to keep the site dry and workable.
Additionally, surface drains like gutters and downspouts must be part of the system design, especially for commercial roofs. We coordinate these elements to create a comprehensive water management system that functions effectively throughout construction and beyond.
Step 3: Foundation Waterproofing Application
The foundation is one of the most vulnerable parts of any building when it comes to water damage. Waterproofing construction demands applying specialized protective barriers to the foundation walls and slabs. We use proven methods such as bituminous coatings, liquid-applied membranes, and waterproofing sheets.
Our teams prepare the surfaces by cleaning and repairing any defects, ensuring maximum adhesion of the waterproofing material. We carefully apply the selected membrane in multiple layers, sealing every joint and seam. This prevents water from seeping into the concrete, which can cause cracking, spalling and mold development.
In some projects, we recommend additional protective boards over the waterproof membrane to shield it from damage during backfilling. This step is essential for long-term durability and foundation integrity.
Step 4: Sealing Critical Penetrations and Joints
Even with a solid foundation membrane, water can infiltrate through penetrations like pipes, conduits, or expansion joints. Sealing these vulnerable points is a crucial step in waterproofing construction.
Get Started
For any questions or concerns, get in touch with our knowledgeable staff today. We would be glad to assist you!
Contact Us TodayWe use flexible sealants, specialized flashing tapes, and preformed seals designed to accommodate building movement without cracking. We carefully inspect every pipe sleeve, utility penetration, and joint to ensure a tight, waterproof fit.
In addition to sealants, we install metal flashings or sheet metal components around openings to divert water away and add a physical barrier. This step is vital in commercial buildings where numerous utilities penetrate the building envelope.
Step 5: Exterior Wall Waterproofing and Protection
Waterproofing construction extends beyond the foundation—it includes the exterior walls, especially in areas exposed to rain, wind-driven moisture, or splashback. Michaels Sheet Metal advises applying water-resistant coatings or membranes on exterior walls, particularly on below-grade portions or masonry walls.
For buildings with flat roofs or parapet walls, proper flashing installation and sealing at roof-to-wall intersections are critical. We also recommend cladding or siding systems that incorporate weather barriers to prevent moisture penetration while allowing the walls to breathe.
When metal roofing or sheet metal components are part of the building, we fabricate and install precise flashing details that integrate seamlessly with wall membranes. This integrated approach reduces water infiltration risk at joints and terminations.
Step 6: Continuous Inspection and Maintenance During Construction
Waterproofing construction is not a “set and forget” process. Throughout the project, Michaels Sheet Metal maintains continuous inspection routines to ensure the waterproofing systems are installed correctly and remain intact during subsequent construction phases.
We coordinate with site managers to protect waterproof membranes from damage caused by trades people, equipment, or weather exposure. Temporary coverings and barriers are often used to shield vulnerable areas until final cladding and roofing are in place.
Regular inspections include checking drainage functionality, verifying sealant conditions, and monitoring any water intrusion signs. Early detection and repair of issues minimize costly delays and preserve the integrity of the waterproofing system.
Why Waterproofing Construction Matters for Your Project
Every step in the waterproofing process adds a layer of protection that safeguards your investment. At Michaels Sheet Metal, we’ve witnessed projects where inadequate waterproofing led to foundation cracks, interior leaks, and mold infestations—all preventable with proper protocols.
Waterproofing construction on a building site is a multidisciplinary effort involving engineering expertise, skilled craftsmanship, and proactive project management. Following these six steps ensures your building stands resilient against water damage for decades.
FAQs
- 1. What is the difference between waterproofing and damp-proofing on a construction site?
Waterproofing provides a complete barrier to water penetration, protecting structures from liquid water under pressure. Damp-proofing primarily prevents moisture vapor but is less effective against liquid water. Michaels Sheet Metal recommends waterproofing in critical areas like foundations for comprehensive protection. - 2. How soon should waterproofing be applied during construction?
Waterproofing should begin immediately after foundation work and before backfilling. Exterior wall waterproofing starts once the structural shell is in place. Early application prevents water damage during rainy periods and keeps the site safe. - 3. Can waterproofing systems be repaired if damaged during construction?
Yes, but repairs can be costly and time-consuming. We prioritize protecting waterproofing layers during construction and perform immediate repairs if damage occurs to maintain system integrity. - 4. Are there eco-friendly waterproofing materials available?
Yes. Some liquid-applied membranes and coatings use low-VOC formulations and sustainable components. Michaels Sheet Metal evaluates environmental impacts when selecting products to balance performance with sustainability. - 5. How do you ensure waterproofing solutions comply with local building codes?
We stay up-to-date on all local, state, and industry regulations. Our team integrates code requirements into the waterproofing plan, obtains necessary permits, and coordinates inspections to guarantee compliance.