Innovative Techniques for Custom Sheet Metal Fabrication at Michaels Sheet Metal
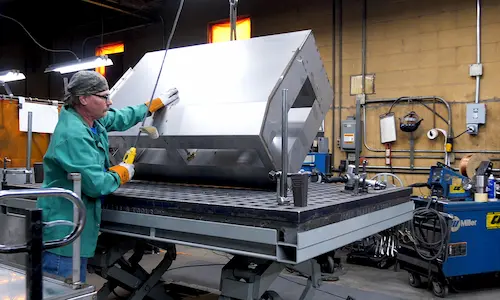
At Michaels Sheet Metal, we weave our commitment to excellence into every metal sheet we craft. As a leading name in the industry, we take pride in pushing the boundaries of innovation, consistently delivering bespoke sheet metal solutions that meet and exceed the unique needs of our clients.
This article delves into the innovative techniques that set Michaels Sheet Metal apart in custom sheet metal fabrication.
1. Cutting-Edge Design Technology:
In the dynamic landscape of sheet metal fabrication, staying ahead requires embracing cutting-edge design technologies. At Michaels Sheet Metal, we leverage state-of-the-art computer-aided design (CAD) software to conceptualize and refine our projects with unparalleled precision. This technology streamlines our design process and allows us to create intricate and complex patterns, ensuring the final product meets the most demanding specifications.
2. Precision Laser Cutting:
One of the cornerstones of our innovative approach is precision laser cutting. Our advanced laser-cutting machinery enables us to achieve intricate and accurate cuts on various metals, from stainless steel to aluminum. This technique not only enhances the efficiency of the fabrication process but also ensures a superior level of detail in the final product. Michaels Sheet Metal takes pride in pushing the boundaries of what is possible through the precision of laser cutting technology.
3. Automated Forming Processes:
In our pursuit of perfection, Michaels Sheet Metal has embraced automated forming processes. Our cutting-edge machinery utilizes computer numerical control (CNC) technology to shape and mold sheet metal accurately. This accelerates production times and minimizes the margin for error, resulting in consistently high-quality fabricated components. As a company, investing in automation is investing in the precision and reliability of our craftsmanship.
4. Versatile Welding Techniques:
Welding is the backbone of sheet metal fabrication, and at Michaels Sheet Metal, we employ a range of versatile welding techniques. From Tungsten Inert Gas (TIG) welding for its precision in thin materials to Metal Inert Gas (MIG) welding for efficiency in thicker sections, our skilled welders adapt their expertise to the unique requirements of each project. Our commitment to versatility ensures that we can handle various materials and project complexities.
5. Innovative Finishing Touches:
The journey from raw metal sheets to the final product is incomplete without meticulous finishing touches. Michaels Sheet Metal embraces innovative finishing techniques to enhance both aesthetics and functionality. Whether it’s powder coating for durability, polishing for a flawless appearance, or custom paint finishes to match specific branding requirements, our finishing touches are a testament to our commitment to delivering a product that meets and exceeds expectations.
6. Continuous Research and Development:
Innovation is a journey, not a destination. At Michaels Sheet Metal, we understand the importance of continuous research and development to stay at the forefront of our industry. Our team actively explores emerging technologies, materials, and techniques to elevate our custom sheet metal fabrication processes. This commitment ensures that our clients benefit from the latest advancements in the field.
Michaels Sheet Metal is a beacon of innovation in custom sheet metal fabrication. Our dedication to cutting-edge design technology, precision laser cutting, automated forming processes, versatile welding techniques, and innovative finishing touches sets us apart. As we continue to evolve through continuous research and development, our clients can trust us to turn their unique visions into tangible, high-quality sheet metal masterpieces.