Quality Control in Custom Metal Fabrication: Best Practices for Superior Results
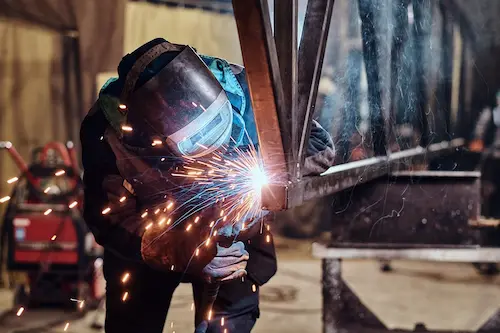
Every project we undertake demands precision, durability, and strict adherence to client specifications. Our approach ensures that fabricated metal components meet the highest standards of excellence. Implementing rigorous quality control measures is essential to achieving superior results.
Understanding Custom Metal Fabrication Quality Control
Quality control in custom metal fabrication is the systematic process of ensuring that every piece produced meets the required specifications and industry standards. It involves a series of checks and balances throughout the fabrication process, from material selection to final inspection. Our quality control measures at Michaels Sheet Metal help eliminate defects, minimize errors, and ensure consistency across all projects.
Material Selection and Inspection
The foundation of high-quality fabrication begins with selecting the right materials. Using substandard metals can compromise structural integrity and result in premature failures. At Michaels Sheet Metal, we source only premium-grade metals that align with project requirements. Our process includes:
1.Verifying material certifications and compliance with industry standards.
2.Conducting thorough inspections for defects such as cracks, rust, or inconsistencies.
3.Testing metal properties, including tensile strength, corrosion resistance, and weldability.
Precision in Cutting and Shaping
Cutting and shaping are critical steps in custom metal fabrication. Any inaccuracies at this stage can lead to assembly issues and wasted materials. To maintain the highest level of precision, we utilize:
1.CNC (Computer Numerical Control) cutting for exact dimensions and intricate designs.
2.Laser cutting for smooth, accurate edges with minimal material waste.
3.Waterjet cutting for heat-sensitive metals to prevent warping or distortion.
Welding Standards and Inspection
Welding is vital in custom metal fabrication, as it joins metal components into a cohesive structure. Poor welding can lead to weak joints, compromising the durability of the final product. At Michaels Sheet Metal, our welding process includes:
1.Using certified welders trained in multiple welding techniques, including TIG, MIG, and spot welding.
2.Ensuring proper heat control to prevent warping and structural weaknesses.
3.Conducting visual inspections, X-ray testing, and ultrasonic testing for weld integrity.
Dimensional Accuracy and Tolerance Checks
Meeting exact specifications is crucial in custom metal fabrication. Even minor deviations can affect functionality and compatibility. Our quality control process includes:
1.Using precision measuring instruments such as calipers, micrometers, and coordinate measuring machines (CMMs).
2.Conducting regular in-process inspections to detect deviations early.
3.Implementing statistical process control (SPC) methods to maintain consistency.
Surface Finishing and Coating
Surface finishing enhances both the appearance and durability of fabricated metal parts. The right finish prevents corrosion, improves adhesion for coatings, and meets aesthetic requirements. At Michaels Sheet Metal, we offer:
1.Sandblasting and grinding to remove imperfections.
2.Powder coating for superior durability and resistance to wear.
3.Anodizing and galvanizing for enhanced corrosion resistance.
Assembly and Final Inspection
Before delivering any project, we conduct thorough assembly checks to ensure all components fit precisely. Our final inspection process involves the following:
Get Started
For any questions or concerns, get in touch with our knowledgeable staff today. We would be glad to assist you!
Contact Us Today1.Verifying all dimensions against design specifications.
2.Checking for proper alignment and secure fastening of components.
3.Testing mechanical and functional performance to confirm reliability.
Compliance with Industry Standards
At Michaels Sheet Metal, adherence to industry standards is non-negotiable. We comply with:
1.American Welding Society (AWS) standards for welding quality.
2.International Organization for Standardization (ISO) guidelines for manufacturing excellence.
3.Occupational Safety and Health Administration (OSHA) safety requirements.
Employee Training and Continuous Improvement
A strong quality control program is only as effective as the team implementing it. We prioritize ongoing training and skill development for our fabricators, welders, and inspectors. Our approach includes:
1.Regular training sessions on the latest fabrication techniques and equipment.
2.Encouraging a culture of accountability and precision among team members.
3.Implementing feedback loops to refine and enhance our processes continuously.
Technology Integration for Enhanced Quality Control
Advancements in technology have transformed custom metal fabrication, making quality control more efficient and precise. At Michaels Sheet Metal, we leverage:
1.Automated inspection systems that detect inconsistencies with high accuracy.
2.3D modeling and simulation software to visualize and verify designs before fabrication.
3.Digital tracking systems to monitor and document quality control data in real time.
Ensuring Client Satisfaction
Ultimately, our quality control measures aim to exceed client expectations. Custom metal fabrication projects often involve tight tolerances and unique specifications, requiring a meticulous approach. By maintaining rigorous quality control, we ensure:
1. Reduced rework and material waste.
2.Faster turnaround times without compromising quality.
3.Reliable, high-performance metal components tailored to client needs.
We are committed to delivering superior custom metal fabrication solutions. Our emphasis on quality control guarantees precise, durable, high-quality results for every project.
Need high-quality custom metal fabrication? Contact Michaels Sheet Metal for precision work and exceptional results today!